Sealing Technologies in Glass Jars: Ensuring Freshness and Longevity
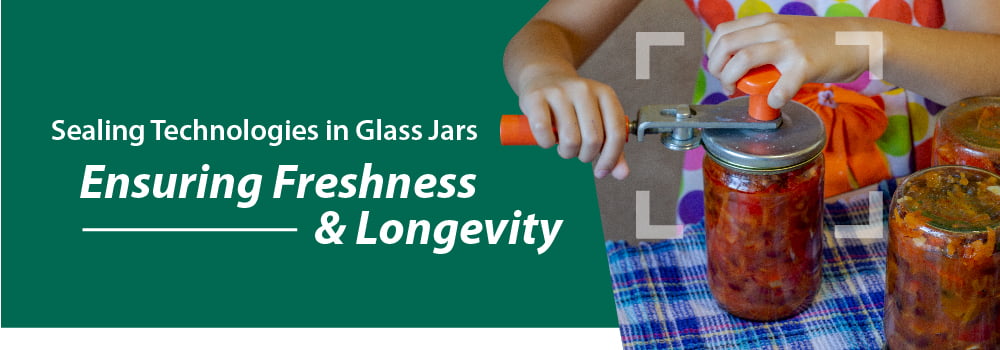
In the arena of food and beverage packaging, glass jars have been a preferred choice for centuries due to their purity, safety, inertness, and the ability to preserve the quality of their contents.
Sealing technology is a crucial, yet often overlooked, aspect of glass jar packaging. Its importance cannot be overstated.
Appropriate sealing technologies are essential not only for preserving freshness but also for enhancing the longevity and safety of the products stored within.
Let’s examine various sealing options, their advantages, and what’s new in this area of packaging solutions.
The Importance of Sealing in Glass Jars
Sealing is not just a process, but a vital component of glass jar packaging. It plays a crucial role in maintaining the integrity and quality of the product inside.
In the case of liquids, it prevents leakage and wastage.
Choosing the right sealing technology is not just important, it’s paramount. It directly influences product safety, consumer satisfaction, and regulatory compliance.
The proper seal ensures that the product remains fresh from the time it is packaged until it reaches the consumer’s table, instilling a sense of confidence in the product’s quality and freshness.
Types of Sealing Technologies
Several sealing technologies are employed in the packaging of glass jars, each offering unique benefits depending on the product type and intended use. Below are some of the most commonly used sealing technologies in the industry:
- Metal Lug Caps
Metal lug caps are widely used in the food industry to seal glass jars containing products such as jams, sauces, and canned goods. These caps feature small lugs around their circumference, which engage with the jar’s threads to create a secure seal. The sealing process involves heating both the jar and the cap, causing the metal to expand. As the jar cools, it forms a vacuum seal, effectively preserving the contents.
Advantages
- Provides a strong, tamper-evident seal.
- Suitable for high-temperature processing, such as pasteurization.
- Cost-effective and widely used in commercial packaging.
- Twist-Off Caps
Twist-off caps are another popular sealing method, especially for pickles, condiments, and beverages. These caps have a plastisol liner, a thermoplastic material that melts during the capping process and conforms to the jar’s rim, creating an airtight seal. Twist-off caps are favored for their ease of use and reliable sealing properties.
Advantages:
- User-friendly, easy to open and close.
- Provide excellent barrier protection against contaminants.
- Ideal for products requiring frequent use.
- Screw-On Caps with Induction Seals
Screw-on caps with induction seals are commonly used for products requiring long-term storage and tamper evidence, such as pharmaceutical products and high-end sauces. The sealing process involves placing a foil liner on the jar’s mouth, which is then heated by an induction coil to bond with the jar’s surface, creating an airtight seal.
Advantages:
- Ensures a high level of tamper evidence.
- Provides a robust barrier against moisture and oxygen.
- Suited for a variety of products, it includes those sensitive to exposure to the environment.
- Plastic Lids with Rubber Gaskets
Plastic lids with rubber gaskets are often used for non-food items and some food products. The rubber gasket provides a tight seal by compressing against the jar’s rim when the lid is screwed on. This sealing method is ideal for products that do not require high-temperature processing or long-term storage.
Advantages:
- Cost-effective and lightweight.
- Easy to apply and remove.
- Provides adequate sealing for many applications.
- Heat-Sealed Liners
Heat-sealed liners are used with metal or plastic caps to provide an additional sealing layer. These liners are made from heat-sensitive materials that bond to the jar’s rim when exposed to high temperatures, offering extra protection against leakage and contamination.
Advantages:
- Enhances the overall seal integrity.
- Provides an extra layer of protection against leaks.
- Suitable for a variety of products, including those with varying viscosities.
Factors Influencing Seal Performance in Glass Jars
The performance of seals in glass jars is influenced by several factors, all of which must be carefully managed to ensure product safety and longevity:
- Jar and Cap Compatibility: The compatibility between the jar and cap is crucial for achieving an effective seal. Variations in thread dimensions, material properties, and design can impact the sealing process.
- Processing Conditions: The conditions under which sealing occurs, such as temperature, pressure, and duration, significantly affect the seal’s effectiveness. Precise control of these conditions is essential for achieving a reliable seal.
- Material Properties: The materials used in the seal and the jar must be compatible and durable enough to withstand the intended use, including exposure to different temperatures, pressures, and product contents.
- Surface Condition: The cleanliness and smoothness of the jar’s sealing surface are vital for ensuring a uniform and effective seal. Contaminants or irregularities on the surface can compromise seal integrity.
- Environmental Conditions: Temperature fluctuations, humidity, and pressure changes can affect the performance of seals. Manufacturers must consider these factors when designing and selecting sealing technologies.
Innovations in Sealing Technologies
The packaging industry is continually innovating to improve seal performance and sustainability. Some of the recent advancements in sealing technologies for glass jars include:
- Biodegradable Seals: With the increasing environmental responsibility, seals made from biodegradable materials are gaining traction. These seals decompose naturally, reducing environmental impact.
- Smart Seals: IoT-enabled seals and QR code integrations allow real-time monitoring of seal integrity and product freshness, enhancing transparency and traceability for consumers.
- Resealable Seals: Innovations in seal design have led to resealable options that allow consumers to open and close jars multiple times while maintaining product freshness, particularly useful for products used over an extended period.
The Impact of Sealing Technologies on the Packaging Industry
Advancements in sealing technologies are not only enhancing product preservation but also opening up new opportunities across various segments of the packaging industry. As consumer demand for high-quality, sustainable, and convenient packaging solutions rises, manufacturers increasingly focus on developing seals that meet these evolving needs.
For example, sustainable packaging has driven the adoption of glass jars with eco-friendly sealing options. Similarly, integrating smart technology in seals provides brands with new ways to engage with consumers and ensure product safety.
Moreover, as the demand for premium and artisanal products grows, using advanced sealing technologies in glass jars is becoming a key differentiator for brands looking to stand out in a competitive market. Sealing Technologies are taking the front seat in shaping the future of packaging; therefore, this trend is expected to continue.
Conclusion
Sealing technologies are critical to glass jar packaging, ensuring product safety, freshness, and longevity. With materials, design, and technology advancements, seals are becoming more effective, sustainable, and user-friendly. As the packaging industry continues to innovate, the role of sealing technologies in glass jars will only become more significant, offering new opportunities for brands to meet consumer expectations and drive growth in an increasingly competitive market. Whether for food, beverages, or pharmaceuticals, the right sealing technology is essential for maintaining the quality and integrity of products, making it a key consideration in packaging design and choice.
Sealing technologies in beverages, particularly in glass bottles like those used by Coke and Pepsi, are critical for ensuring product quality, safety, and shelf life. Here are some of the primary sealing technologies used:
- Crown Caps
- Description: Crown caps, also known as crown corks, are the most common type of sealing for carbonated beverages in glass bottles.
- Material: Typically made of metal (steel or aluminum) with a plastic or rubber liner.
- Function: The cap is crimped around the top of the bottle, creating a tight seal. The liner provides an additional barrier to keep the carbonation inside and contaminants out.
- Advantages:
- Excellent sealing capability for carbonated drinks.
- Relatively inexpensive.
- Easy to apply and remove.
- Disadvantages:
- Single-use, which means they create waste.
- Requires a bottle opener.
Swing Top (Grolsch) Closures
- Description: Swing top closures consist of a ceramic or plastic stopper attached to a metal lever system.
- Material: Typically ceramic or plastic with a rubber gasket.
- Function: The stopper is pressed into the bottle opening, and the lever system creates a tight seal.
- Advantages:
- Reusable and resealable.
- Provides an excellent seal for both carbonated and non-carbonated beverages.
- Disadvantages:
- More expensive than crown caps and screw caps.
- Requires more effort to manufacture and apply.